PVC制品调好配方的关键
一、各种润滑剂对PVC塑化快慢的影响对比
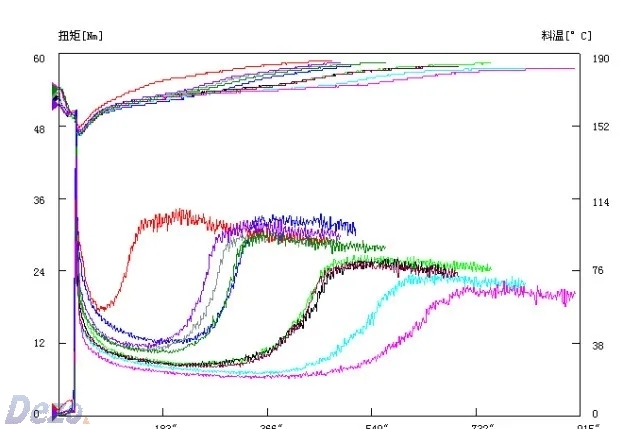
由上图流变得出硬脂酸钙塑化最快,单甘脂次之,60再次之,再次是硬脂酸铅、氧化聚乙烯蜡,硬脂酸,PE蜡,石蜡塑化最慢。增塑剂环氧大豆油对于改善熔体流动性的作用比较明显。
润滑剂一般同时具有内润滑跟外润滑的特性,而不能绝对来说具有单一性能。从使用效果来说,极性越大,跟PVC相容性越好,增加PVC分子间流动性效果越明显,内润滑性占主导,相反,非极性越突出,外润滑性占主导。
实际应用中,常用润滑剂硬脂酸钙、单甘脂、PETS、60、16等的内润滑性比较突出;PE蜡、石蜡、74等的外润滑性比较突出。硬脂酸、316系列氧化聚乙烯蜡,内外润滑性均沾,316系列脱模性比较好。
二、润滑剂为什么会析出?
1、内润滑多了,流动性很好,塑化时间变短,但是多余的内润滑会转变成外润滑效果,造成析出,例如硬脂酸、硬脂酸钙造成的析出及结垢问题;
2、外润滑多了,塑化变差,变慢,因为跟PVC相容性差,加多后会造成严重析出;
3、润滑剂中的小分子物质影响,举个很经典的例子,单甘脂,本身单甘脂是一种很好的内润滑剂,但是由于厂家生产过程中为降低成本,添加多量的甘油,造成单甘脂中含有很多甘油成分,甘油分子量低,很容易在PVC加工过程中的析出,实际好的单甘脂添加量正确,是不会造成析出的。
当然,内外润滑也不能太少,讲求内外润滑平衡。内润滑太少,流动性不好,塑化时间延长,扭矩大。外润滑太少,流体发粘,造成糊料或者光泽度不够等现象。
三、润滑剂的协同应用
润滑剂熔点不同,内外润滑效果不同,跟PVC相容性不同。因此一个完美的PVC配方中往往需要多种润滑剂配合使用,以达到理想的效果。
熔点低的润滑剂初期效果较好,这类润滑剂有石蜡、硬脂酸丁酯、硬脂醇、多元醇酯类、硬脂酸等。
熔点适中的润滑剂,熔点范围大约100-125度,作为中期润滑,这类润滑剂有硬脂酸铅、硬脂酸镉、PE蜡、OPE蜡等。
熔点高的润滑剂一般作为后期润滑使用,这类润滑剂有硬脂酸钙、硬脂酸钡、316等。
配方中单独使用硬脂酸钙,可加速塑化,提高熔体粘度,增大转矩,并具有一定脱模效果,而单独使用石蜡,表现出延迟塑化,降低转矩,无脱模作用.将硬脂酸钙和石蜡(聚乙烯蜡)按一定比例混合使用时,表现出了良好的效果,物料转矩值可降低很多,这是由于石蜡渗入硬脂酸钙分子间,强化了润滑作用,表现出很强的协同效果。相同作用的还有硬脂酸与石蜡。
在实际生产中我们最常见到的组合是60+74,16+74/70s,60+316+PE蜡,硬脂酸+硬脂酸钙+石蜡+PE蜡,硬脂酸+PE蜡,硬脂酸+石蜡,60+316+石蜡+PE蜡+硬脂酸钙等
在PVC配方中使用多种润滑剂,互相渗透,弥补温差,不仅可以减少润滑剂的使用总量,还能使PVC配方料的加工范围变宽,提高PVC熔体结构的均匀性,提高材料的力学性能和外观质量,保证物料挤出过程的润滑平衡。
四、润滑剂的稳定作用和协同性
部分润滑剂如脂肪酸皂类,本身具有热稳定作用,润滑剂添加后降低了加工时的物料温度,所以对热稳定具有良好的作用,如白色制品硬脂酸加入后明显比不加颜色更白。单甘脂、季戊四醇酯等具有螯合作用,减少了PVC的催化分解。
铅盐稳定剂,极性强的润滑剂与PVC相容性更好。有机锡本身具有一定的增塑作用,物料塑化较快,注意协同配合塑化慢一些的润滑剂。稀土稳定剂本身与润滑剂协同作用较好,能促进物料熔融塑化。
PVC制品配方的关键就在于润滑剂,也是配方中最难的部分,软硬度的调整只需要调整增塑剂用量即可,稳定剂的用量基本是一个定值,唯独的变量就是润滑剂,使用对了,产品力学性能好,表面关泽度强,连续生产时间长。配合不好,大了挤不出正常产品,小了说产品力学性能变差,制品发黄,蝴蝶斑,波浪纹、鱼鳞纹,蝴蝶斑等,因此润滑剂的作用不可小觑。
五、如何判断内、外润滑平衡
(1) 内、外润滑均不足。特点是熔体粘度较大,塑化扭矩较大,熔体粘壁现象严重,内表面不光滑;表现在转子上熔融实验料不好清理。严重的有可能提前热分解,制品力学性能较低。如果内、外润滑平衡,其熔融试验料一碰就下来,转子表面基本不粘熔体料。(2) 内、外润滑剂均过量。塑化扭矩较小,有析出现象,虽然试样光滑度很好,但力学性能较低,易脆,严重时用手擦拭试样有油样感觉。(3) 内润滑剂较少、外润滑剂较多。塑化时间明显地延长,由于内润滑剂较少,树脂内摩擦力较大,也容易造成热分解。塑化扭矩有所增大,有时用手感觉试样表面有涂油的感觉,试样变脆。(4) 内润滑剂较多,外润滑剂较少。塑化时间明显地缩短,使树脂提前塑化,造成高黏度熔体受到剪切力作用的时间过长,同时有较严重的黏附现象,转子不好清理,也造成了热稳定时间缩短,制品或试样有分解黄线。 总之,外润滑剂用量不足则有黏附现象,塑化时间短,试样表面不光滑;外润滑剂过量则塑化时间明显延长,力学性能下降,变脆,可能有析出现象,严重时手拭有油样感觉。内润滑剂用量不足则塑化扭矩较大、塑化时间较长;内润滑剂过量则塑化时间较短、塑化扭矩较小,但热稳定时间也变短,有热分解现象,试样内壁不光滑。 研究与实践均表明,一般情况当塑化度60%时,拉伸强度最高;当塑化度65%时,冲击强度最高;当塑化度70%,断裂伸长率最高;另外,出于多种原因的考虑,不同制品对塑化程度均有不同要求。不完全塑化,不仅质量好,产量高,能耗低,还可以降低热稳定剂用量,有利于生产成本的降低。在充分考虑热稳定剂及其他助剂等因素对润滑作用影响的前提下,通过调整内、外润滑剂的品种与数量,可以调控塑化速率,增加树脂的流动性,改善树脂的黏附性。由于PVC配方是塑料配方中最复杂、所使用小料种类最多的一种,对于调整内外润滑平衡,大家要多摸索多思考,才能掌握调整润滑。
六、UPVC制品润滑体系的判断和调整
首先,是要保证物料在料筒里面有一个比较适合的塑化度,就是在真空口物料能成团或者缠绕(回收料较多的情况下)在螺杆上。这个可以说明,塑化马马虎虎了。如果塑化成团,还要看看塑化团的断面有没有光泽,有没有滋润感,如果没有光泽,塑化还是稍稍欠缺一点的。但是仅凭这一点还不能判定塑化度是否合适,还要根据模具的出料情况和制品的发泡情况来判断。但是如果在真空口看不到料,就可以判断外润滑过量了。如果四区或者五区的温度一直降不下来,或者冷却风扇几乎没有停歇的转动时,也可以马上判定,塑化过头了。
其次,就是从物料在模口的情况来判断了。
从对于发泡产品。从模具出来的物料可以是表面来看,如果表面出现密集的直径一公分甚至更大的鼓包,是塑化不够,应该增加内润滑。如果表面出现很细微的小泡破裂,这是塑化过度,应降低内润滑。这些都是比较极端的情况。如果表面良好,可用拇指来捏板材表面来判断塑化是否正常。如果非常硬,没有弹性,表明外润滑过量,要降低,如果像泥膏状偏软,没有弹性,说明内润滑过量,要适当降低。良好的塑化情况应该是有非常好的回弹性。就是手指一按感觉有弹力,回弹力越大越好,在填充较高的情况下,会按下一个小坑,如果马上会弹的,这时候塑化最好,如果按下一个小坑马上就能回复也算不错,小坑回弹的越慢配方配方越差,如果到出了第一个定型模还不能恢复的,就算比较糟糕了。一般是降低内润滑。这一般是在530用量足够的前提下,或者适当提高530用量。 还可以通过发泡物料离膜膨胀的情况来判断塑化是否恰当,一般塑化合适的配方应该是离开模具后才开始膨胀发泡,其发泡面角度根据不同厚度大致在60-80度左右。如果物料离开模具后一段距离后才开始膨胀,基本可以判断是外滑过量,造成所谓的延迟发泡。 如果物料离开口模口立即发泡,发泡角度很大,让人感觉仿佛在模具里面已经开始发泡似的,即所谓的提前发泡,基本判定是塑化过度,内润滑过多。而且配方调整的结果往往都是走曲线形式的,有时候,同样的一个问题,我减少内润滑,你增加内润滑,都能达到同样的调整效果,这就是所谓的殊途同归。内润滑增加主要是改善物料的流动性,增加内润滑以后,物料整体的流动性加快,中间两侧出料都会加快,但是从高分子流变特性来说,中间流程短,影响更大,就是中间出料会更快一些。 外润滑的作用是减轻物料与模具的摩擦,也能改善流动性,外润滑增加后,物料的出料情况也会改善,但是中间物料流程短,两侧的流程长,相对而言,增加外润滑后,两侧流动加快的程度比中间要高一些,所以总体上表现两侧出料的改善。 内润滑多,中间出料快,外润滑多,两侧除了快。就是说中间出料快的时候,可适当降低内润滑,两边不出料的时候,适当提高外润滑。另外,内外润滑剂对制品表面的影响,很多时候,润滑体系基本上差不多,就是表面还有少许的瑕疵,比如波浪纹,V字水波纹,鲨鱼皮等等。这个时候基本上都是属于润滑剂微调了。 一般情况下,波浪纹出现在中间,往往都是内润滑过量,这个时候按照挤出方向来看,波浪纹,V字纹都是箭头朝前的。往往还伴随着芯层中段有大泡孔、串孔等现象。应该降低内润滑。如果出现在两侧,往往是外润滑过量,这个时候按挤出方向来看,波浪纹,V字纹都是箭头向后的。可适当降低外润滑。所以,内外润滑的调整往往要根据以上几个方面的影响综合评估来进行调整了。七、结论
润滑剂根据其具体作用一般分为内润滑剂、外润滑剂和内外润滑剂。具体表现如下:
1、内润滑少,外润滑多的表现
外润滑剂主要是减少聚合物熔体与螺杆、料筒和模体之间的黏结强度,降低它们之间的摩擦力;塑化所需要时间较长,熔融物料流动性差,塑化扭矩较大,制品力学性能下降,变脆,还可能出现析出现象,严重时用手试有油样的感觉。
2、内润滑多,外润滑少的表现
内润滑剂是降低聚合物分子之间的摩擦力,增加聚合物的加工流动性和均匀性。区分内、外润滑剂的关键是润滑剂与聚合物的相容性,外润滑剂相容性小。塑化时间较短,有较重的粘附现象,制品表面光泽度差,有可能热稳定性变差。
3、小结
外滑过多,挤出速度虽然快,但物料易生,塑化不好; 外滑用量不足,则有粘附现象,塑化时间短; 内滑过量,挤出量大,物料塑化不好,力学性能下降,有可能有析出现象; 内滑用量不足,则塑化扭矩较大,塑化时间较长。 内外润滑剂用量不足。则是塑化扭矩大,熔体粘附性严重,可能发生热分解。 内外润滑剂用量过大。则是析出严重,制品力学性能下降,二次加工性能差。 内润滑剂较少,外润滑剂较多。则塑化时间较长,塑化扭矩大,有析出现象。 内润滑剂较多,外润滑剂较少。则是塑化时间较短,熔体粘附性严重,可能发生热分解。
- 上一篇:连续纤维增强热塑性复合材料在汽车零部件上的 2022/6/28
- 下一篇:单手操作、防纂改、可回收 最新瓶盖技术助力包 2022/6/28